Inscrite au programme Usine du Futur, la PME à potentiel Next, membre du Club des ETI de Nouvelle-Aquitaine, a mis en place des robots collaboratifs (ou cobots) pour réduire la pénibilité du travail des opérateurs. Son Directeur Industriel Stéphane Pradelle (adhérent aux côtés du Président Antoine Pontaillier) partage son expérience et les conditions de réussite de ce projet de transformation.
Basé à Nersac (16), le groupe Next fabrique depuis 1973 des emballages thermoformés pour l’agro-alimentaire et l’industrie, ainsi que des masques de protection. Avec 120 collaborateurs répartis sur trois sites de production, il a réalisé un chiffre d’affaires de 23 M€ en 2022. |
Qu’est-ce qu’un cobot par rapport aux robots industriels que nous connaissons ?
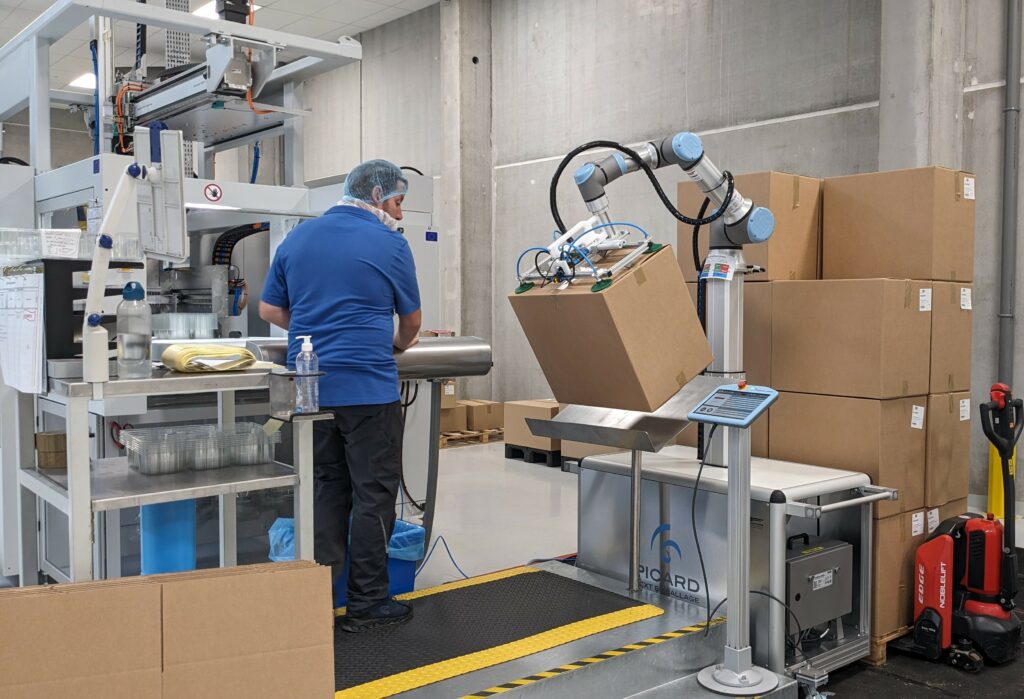
Les robots traditionnels ne collaborent pas mais exécutent des opérations à cycles rapides. Par sécurité, ils travaillent dans des espaces confinés. Les cobots quant à eux sont conçus pour travailler en collaboration avec l’homme en toute sécurité. Ils peuvent réaliser différentes opérations. Dans notre cas, il s’agit d’assurer la palettisation de cartons de produits finis sur palette grâce à des cobots équipés d’un axe télescopique et d’un bras muni d’un préhenseur à ventouse.
D’où est venu le projet d’équiper votre usine de cobots ?
La volonté de Next est de viser l’excellence opérationnelle. C’est dans le cadre des actions d’amélioration de nos activités de thermoformage que nous avons cherché comment supprimer les tâches répétitives, pénibles et fatigantes, pour donner aux opérateurs des missions plus intéressantes et contributives. Nous avons évalué différentes solutions mécaniques pour manipuler et mettre les cartons sur palettes. Mais elles nécessitaient toujours une intervention humaine. L’arrivée de la nouvelle génération de cobots a été la révélation. Les technologies précédentes présentaient des limites de rapidité ou de charge. Les dernières améliorations ont apporté de meilleures capacités, une flexibilité pour permettre aux cobots d’être déplacés d’un poste à l’autre selon les besoins.
Quels sont les facteurs qui ont contribué à la bonne conduite du projet ?
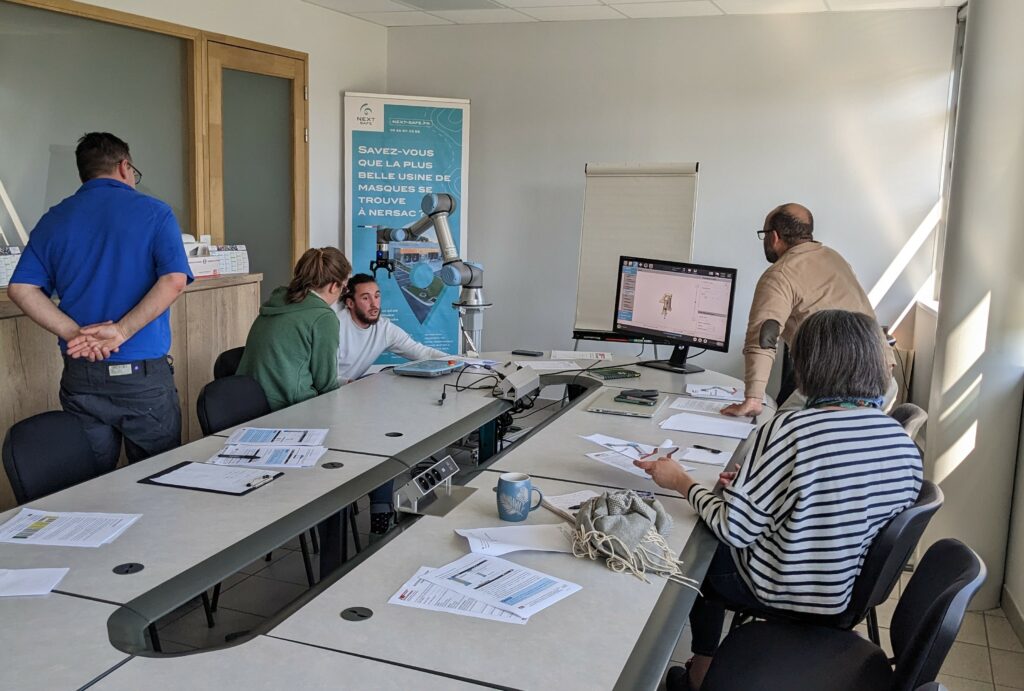
La réflexion a été menée très tôt avec les équipes, qui ont été impliquées dans le projet et la définition des besoins. Nous leur avons expliqué les objectifs, ils ont compris que le projet visait à les soulager, qu’il constituait une aide et pas une contrainte. Les techniciens et opérateurs ont rencontré l’intégrateur, sont allés chez lui pour tester les cobots, ils ont participé à la pré-réception et à la réception des équipements. S’enrichir d’une nouvelle compétence est une valeur ajoutée pour nos salariés, d’autant que la formation est assez simple grâce à une interface sur tablettes intuitive, didactique, presque ludique.
Impliquer, expliquer, écouter et accompagner sur le terrain sont les facteurs clés du succès de ce projet.
Quels bénéfices tirez-vous de cet investissement ? (200 000 € soutenus par la Région Nouvelle-Aquitaine)
Nous n’avons que des retours positifs. Il est encore tôt pour évaluer l’impact sur la production, mais le principal porte sur les conditions de travail et la santé de nos salariés, avec un objectif de réduire voire supprimer les Troubles Musculosquelettiques en améliorant le confort. Les opérateurs ont gagné en valeur ajoutée : le temps qu’ils ne passent pas à décharger, ils le consacrent à la qualité des produits, à l’environnement de la machine. Nous être modernisés contribue aussi à notre image, auprès des clients qui voient que nous investissons dans le futur, et auprès des candidats. Toutes les entreprises n’ont pas de cobots ! Après notre site de Nersac, nous envisageons le déploiement sur nos autres usines. Mais ce projet n’est pas une finalité, nous poursuivons notre évolution, en partageant notre expérience et en nous inspirant des autres entreprises membres du Club !
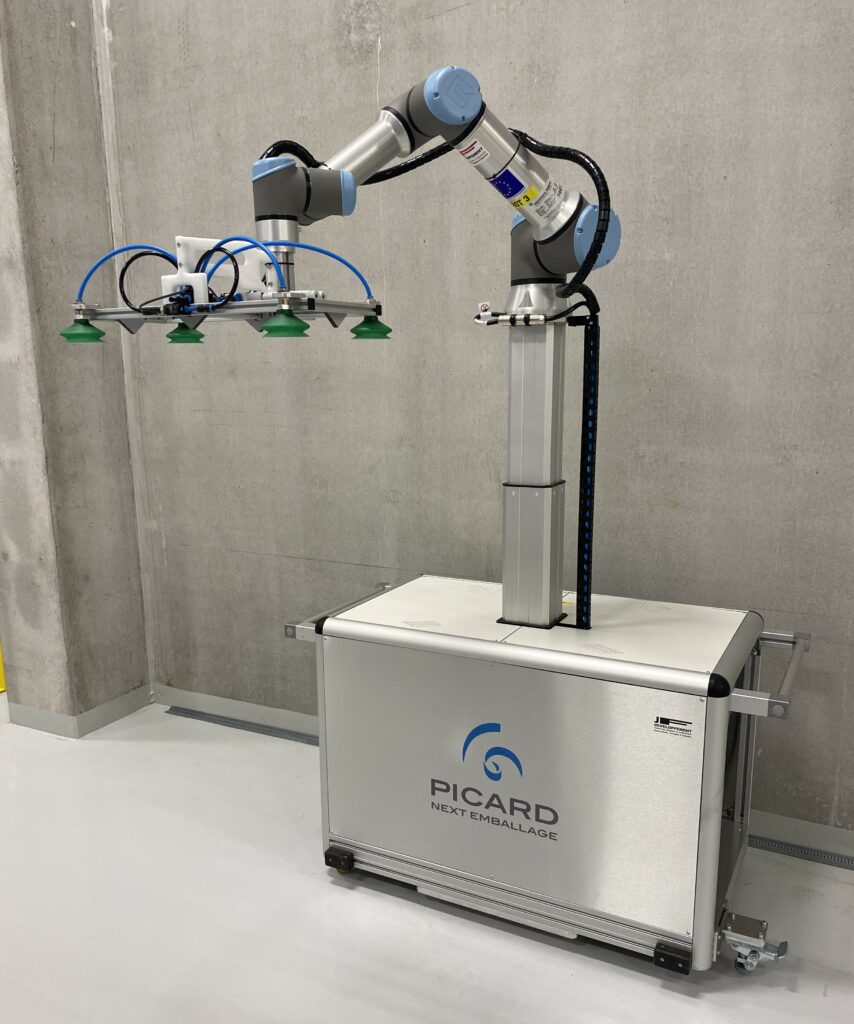